Question & Answers
Responses from the Bus Duct Monitoring Solution webinar on Solving Electrical Outages.
Use the filter buttons to select your area of interest.
Can the bus duct monitoring system be used for cast resin bus duct ?
Currently, no, as there is no access to the joints.
Can the bus duct monitoring system used for medium voltage bus ducts?
Yes, this is suitable for both LV and MV applications as the sensors are mounted on the outside of the bus duct on the joint, which itself is earthed and exposed to touch.
How do you use the bus duct monitoring system at tap off boxes?
The sensors are not designed for monitoring tap off boxes. That would require a different solution. The bus duct monitoring solution is designed (only) to monitor the main bus duct joints themselves. If tap off boxes need to be monitored, a more suitable system would be Exertherm's existing MCC application which is suitable for this type of application.
Can the sensors be installed in high places, or difficult to reach areas, for example, off the ground?
The system can absolutely be installed in such places, this would require access equipmet to install but then it lends itself to being able to monitor those hard to reach areas that conventional thermography couldn’t reach without the need for access equipment which would not be allowed in a live enviroment as trying to carry out such checks from ground level are almost impossible.
Can the sensors be used outside / externally?
Use of the solution outside is possible but it depends on the bus duct type. If the bus duct is a cast resin material then it is unlikely as it it not possible to access the joints as they are cast at site. For other materials, the only point to consider is solar gain, so it is necessary to ensure sensors are not in direct sunlight.
Can the 24 VDC be interconnected via the CAT 6 cable with a maximum distance 120 meters?
Yes, the 24 VDC can be sent down a CAT 6 cable. This potentially could be upto 240 meters in length. Volts will drop down the cable but the units can manage down to 12V DC without issue. Calculations indicate that we should not drop below 18 volts at the last unit.
Is there a standard installation drawing in detail for Exertherm sensors?
Yes, all the installation instructions can be found in the O&M manual for this device.
Can we use the sensors for existing bus bar or only on new bus bars? Because the temperature is outside the bus bar not inside the actual joint.
This can be used on both new and existing bus systems without issues. The temperature is monitored outside the busbar, but a failing or compromised joint transmits the temperature through the bolt and metalwork to the outer plates. Tests prove that a temperature rise is detected within minutes of a problem occuring. A thermographer would inspect exactly the same areas on a joint as they are unable to access the joint with a handheld camera or device.
How long should the distance be between the sensor and bus duct?
The standard sensor loom of 8 sensors has a distance between sensors of 10 feet, so this aligns with standard bus duct lengths.
What is the distance from the DC connection to the first sensor?
At the moment the distance is 5 metres. This allows you to mount the datacards either in the piece of switchgear the bus duct is connected to or the option to have a wall mounted enclsoure nearby with numerous Bus Duct cards inside, which gives flexibility.
Is it possible to install sensors on existing bus ducts? Will it be an external installation?
Yes, it is possible to install in existing bus ducts, the sensors are all mounted external to the bus duct.
Does the solution need a power supply at each DC box?
This depends on how the system is built. Each card needs a power source, but the solution can utilise enclosures with RJ45 connectors on the outside, which use spare cores to deliver the DC power to each card.
When will the bus duct monitoring system be ready for release?
This product is ready now for testing and install into systems.
Does each sensor have its own alarm?
Each sensor can show an alarm at the card level and via the local LED on the datacard, but each sensor does not have its own LED on the sensor. Obviously, this data can be read through the modbus comms into a SCADA/EPMS system and display on an HMI pinpointing the issue.
What is a typical ROl for this solution?
ROI is always difficult to quantify on any system or device. Similar to a fire alert system, its ROI is ideally never, but pays off if it detects just a single fire. The Bus Duct Monitoring Solution would be the same. The ROI would be instant if it detects a problem. But if we look at it against periodic thermography, the costs of installing the system could payback after a couple of years of scanning, but we also need to think of safety aspect. The solution ensures personnel are aware of the health status of each joint so they can ensure that uptime is kept as high as possible. Also that the personnel are not being put in harms if they have to walk through a facility which could potentially have dangerous joints that may lead to a catstrophic failure.
Is there any case study or history from bus duct solution on site? What can we see in SCADA?
As far as history of the system, this is a new system on the market so there is no data. From a SCADA point of view, you will be able to visualise all joint temperatures, and also which joint has detected the alarm so pinpoint the issue
What time scale do you envisage to get ROI on the installed product?
As mentioned in an earlier answer, the ROI can be instant if it detects an issue or when considering the costs of annual thermography, which could be under 3 years. It's important to also consider the safety aspect of both equipment and personnel as well as ROI.
Does the system require civil defense or utility approvals?
To date, we have installed all the other Exertherm sensors in both military and utility sites without issue.
Are there any product standards in existence that the sensor complies to?
The system is tested and approved to CE, CA, CB and UL testing.
Can the temperature range tolerances be preset?
All alarms on the bus duct datacards can be adjusted by the use of DIP switches on the side of the small datacards and set to suit the needs of the operation.
Is it only the joints that need to be monitored for temperature?
The joints are the weaker areas on a bus duct system as these are the points that are subject to movement via either seismic or building temperature movement. The internal bars on the main lengths are elbows/T's and fixed bars.
Does the solution monitor the actual temperature or relative temperature?
It monitors the actual absolute temperature of each joint. This is then compared internally joint to joint, and averages across the number of joints along with a critical high temperature to give alarm alerts.
Is it possible to receive predictions regarding to temperature readings?
Once the data from day one is captured and then over time, yes, it would be possible to start using AI to predict trends and then potential issues.
With temperature readings, is it possible to translate the data to current readings within the solution?
Not within the solution as this would always be a problem. The ambient temperature within the area would influence the actual bus duct temperature from season to season, so would never be able to predict current load levels.
Does these sensors measure absolute temperature or Delta T?
The sensor monitors absolute temperatures on the joints, and then uses temperatures internally within the datacard to calculate delta's across joint to joint.
With this system is it possible to anticipate a failure by understanding the temperature changes?
Yes, this is exactly what the solution does. Changes of temperature from joint to joint, even season to season, once a set of data has been created
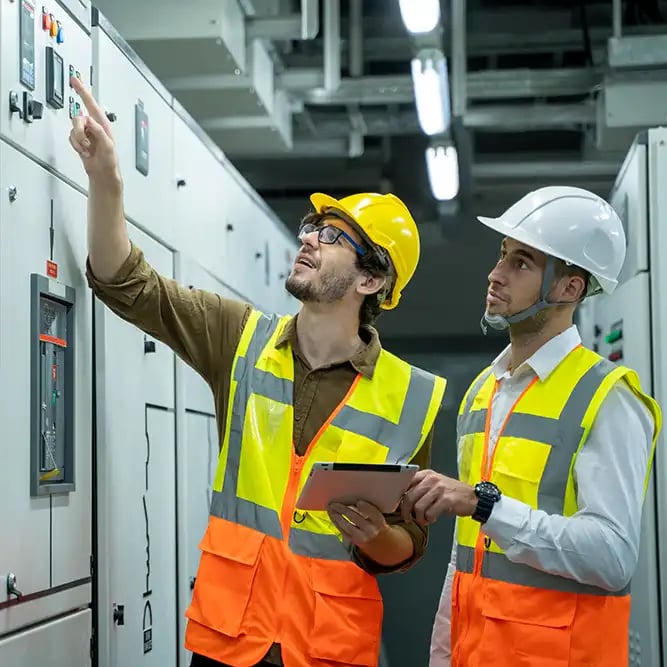