Digitize critical electrical assets
Exertherm ensures robust and secure communication of temperature data without the risk of signal interference or cybersecurity threats.
Exertherm’s sensors provide a direct and continuous view of critical joints or terminations, measuring Delta T (temperature rise over ambient) from within the switchgear enclosure.
Continuous thermal monitoring allows for the early detection of potential issues, reduce unexpected failures and enhancing the overall reliability and safety of electrical systems.
The rising demand for the digitization of mission critical electrical assets and the increasing need for reliable power supply has driven organizations to explore and invest in technologies and solutions that enhance asset reliability. Mission-critical electrical assets are typically found in data centers, manufacturing plants, power distribution networks, and the energy industry. These assets require constant monitoring to help operators prevent failures, optimize performance, and extend their lifespan. The need to ensure asset reliability, personnel safety and operational efficiency is paramount.
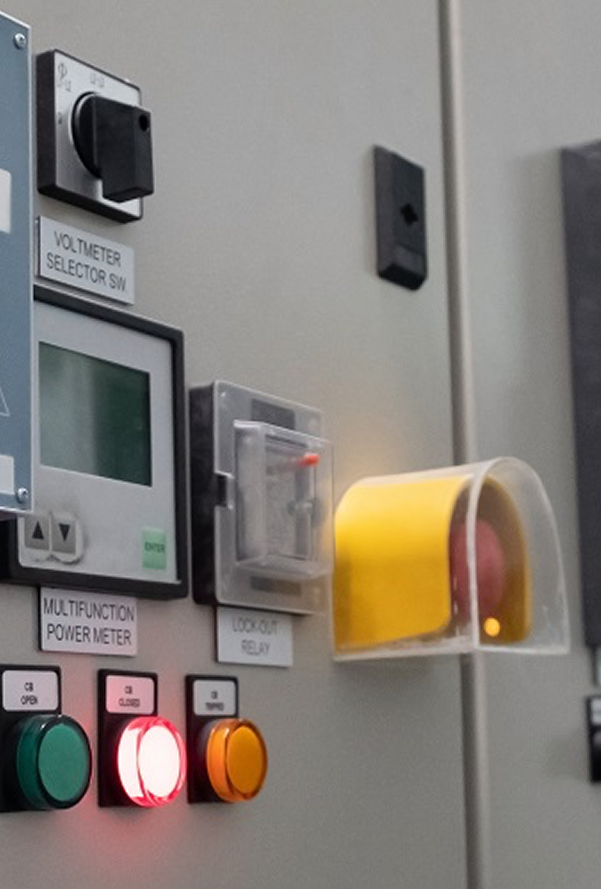
A shift from periodic
maintenance
The evolution of technologies such as Exertherm's Continuous Thermal Monitoring (CTM) sensors have revolutionized the way mission critical electrical assets are monitored and maintained. Traditional periodic maintenance approaches are no longer sufficient in today's fast-paced and sustainability-demanding environments.
Exertherm's CTM solutions stand out from competitive technologies as a result of our continuous innovation in the thermal monitoring space. CTM sensors have made a significant impact on the electrical asset management landscape, with global adoption by some of the largest organizations in the world as they strive to do more with less infrastructure.
Exertherm’s innovative CTM technology sets itself apart from competitors in the ever-evolving space of electrical asset management with numerous cutting-edge benefits that include:
Sensor placement – contactless sensors
One of the standout features of Exertherm’s technology is the use of contactless infrared sensors. Unlike many other sensors in the market that attach directly to conductors, Exertherm’s sensors do not make contact with any conductors. This design choice is crucial for several reasons:
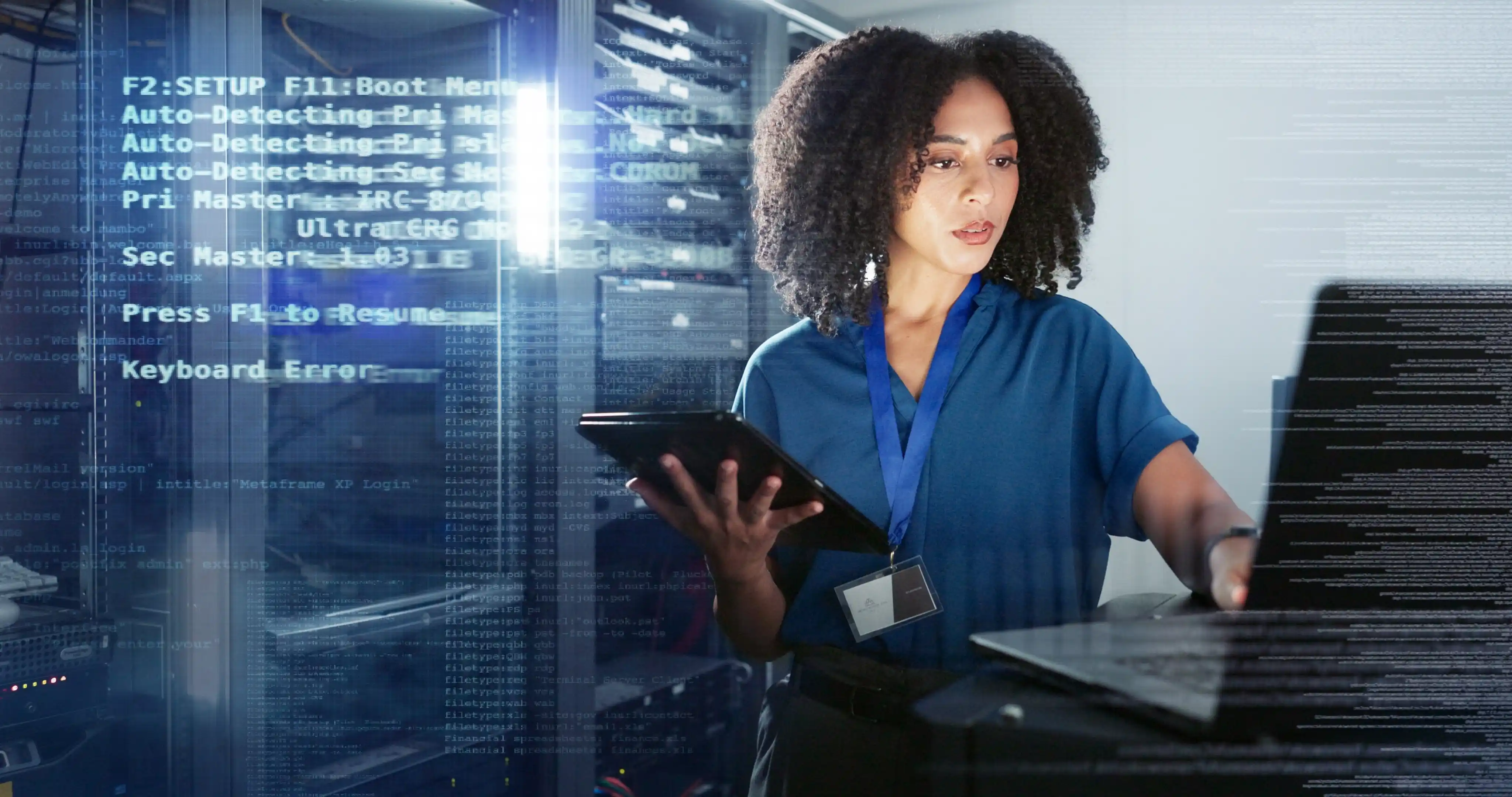
Reduced risk of system weakness
Sensors that attach directly can introduce weaknesses into the power distribution system. They often require different torque settings for bolted joint connections, which can compromise the system’s integrity. Exertherm’s contactless approach eliminates this risk, ensuring a more robust and reliable system.
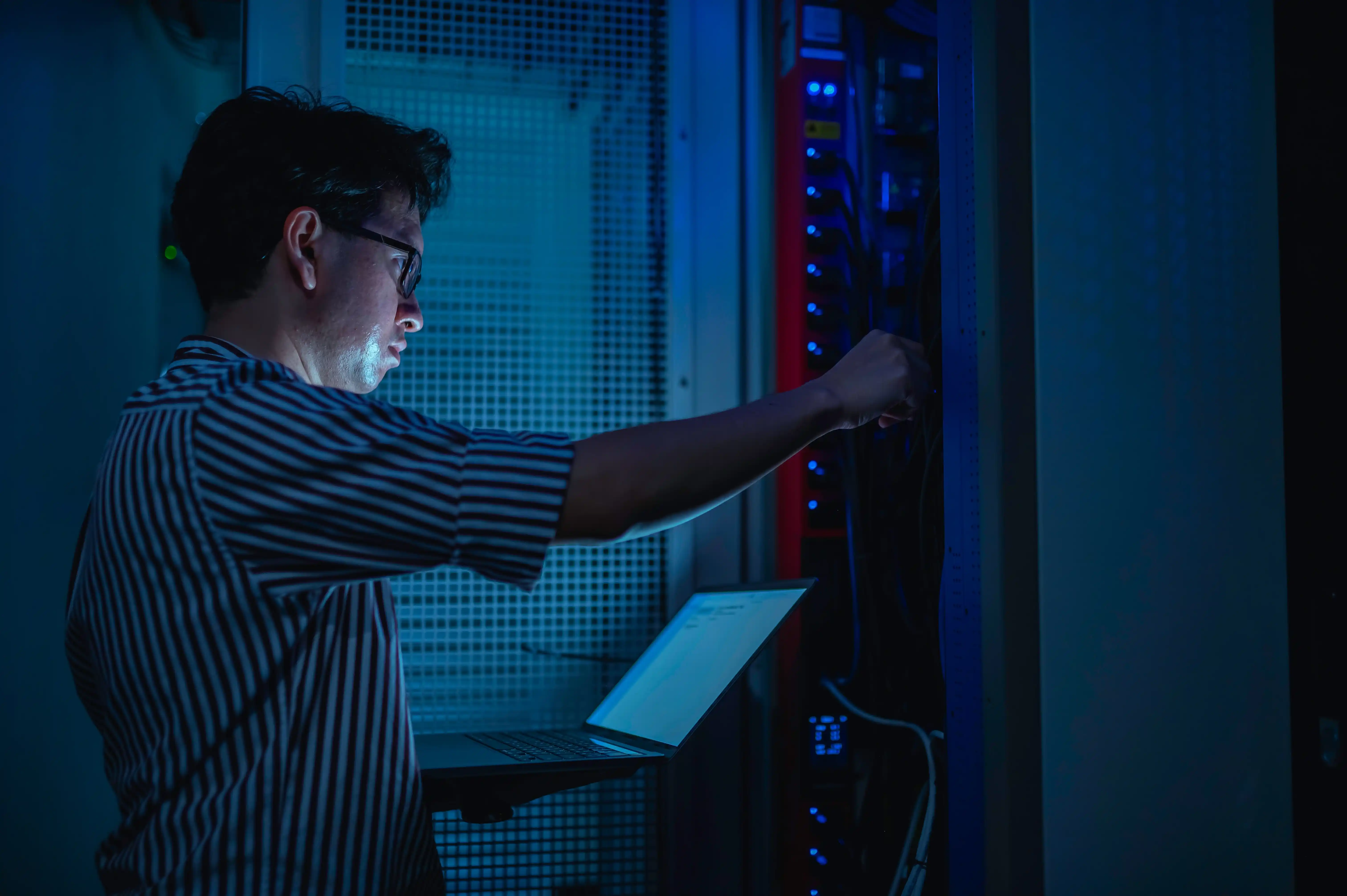
Avoidance of insecure attachments
Sensors attached using Velcro tape or cable ties can lead to insecure connections and longevity issues, becoming a maintenance headache over time. Exertherm’s sensors, fully commissioned at the factory before installation, ensure a secure and reliable setup, minimizing on-site complications and maintenance requirements.

.png?width=35&height=27&name=Vector%20(1).png)
Sensor communication – wired sensors
Exertherm’s sensors are hard-wired, a significant advantage over the wireless alternatives commonly found in the market. Here’s why this matters:
Elimination of antenna requirements
Wireless sensors often require multiple antennas to align RF fields correctly, with transmission distances typically limited to around 30cm under ideal conditions. Exertherm’s hard-wired sensors eliminate the need for antennas, ensuring consistent and reliable communication.
Enhanced
security
Wireless sensors pose a cybersecurity risk due to potential hacking vulnerabilities. By opting for hard-wired sensors, Exertherm ensures robust and secure communication without the risk of signal interference or cybersecurity threats.
Reliable data
transmission
Wireless sensors can suffer from compromised signals due to electromagnetic fields (EMF) and electromagnetic compatibility (EMC) issues. Exertherm’s hard-wired solution guarantees reliable data transmission, free from such interferences.
Sensor powering – non powered sensors
Another significant advantage of Exertherm’s sensors is their ability to operate without an external power source. This feature offers several benefits:
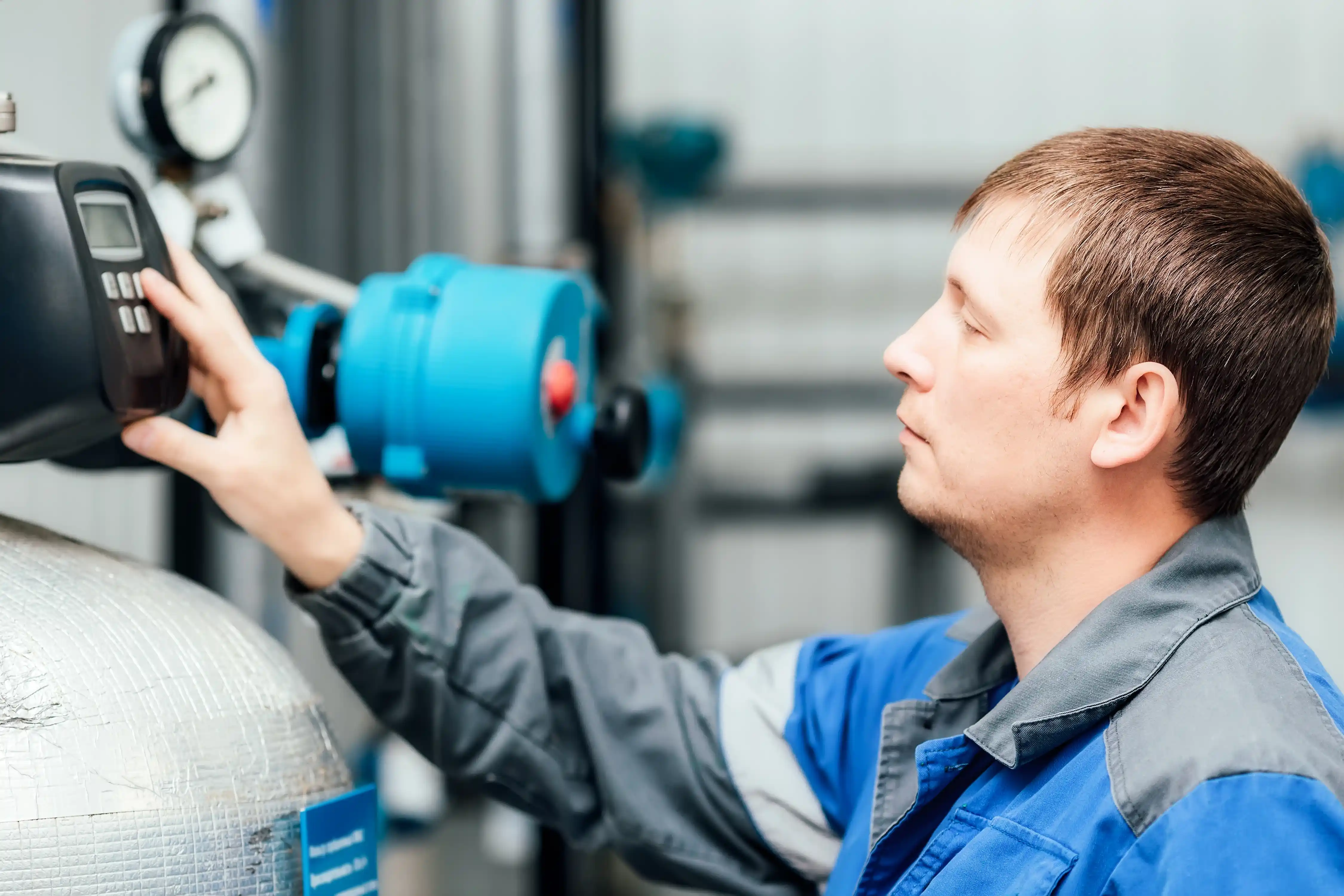
No need for amplifiers
Unlike other sensors that require amplifiers, which can introduce drift and necessitate periodic calibration and costly shutdowns, Exertherm’s sensors derive power directly from the target. This design eliminates the need for external power sources, reducing maintenance requirements and ensuring continuous operation without interruptions.
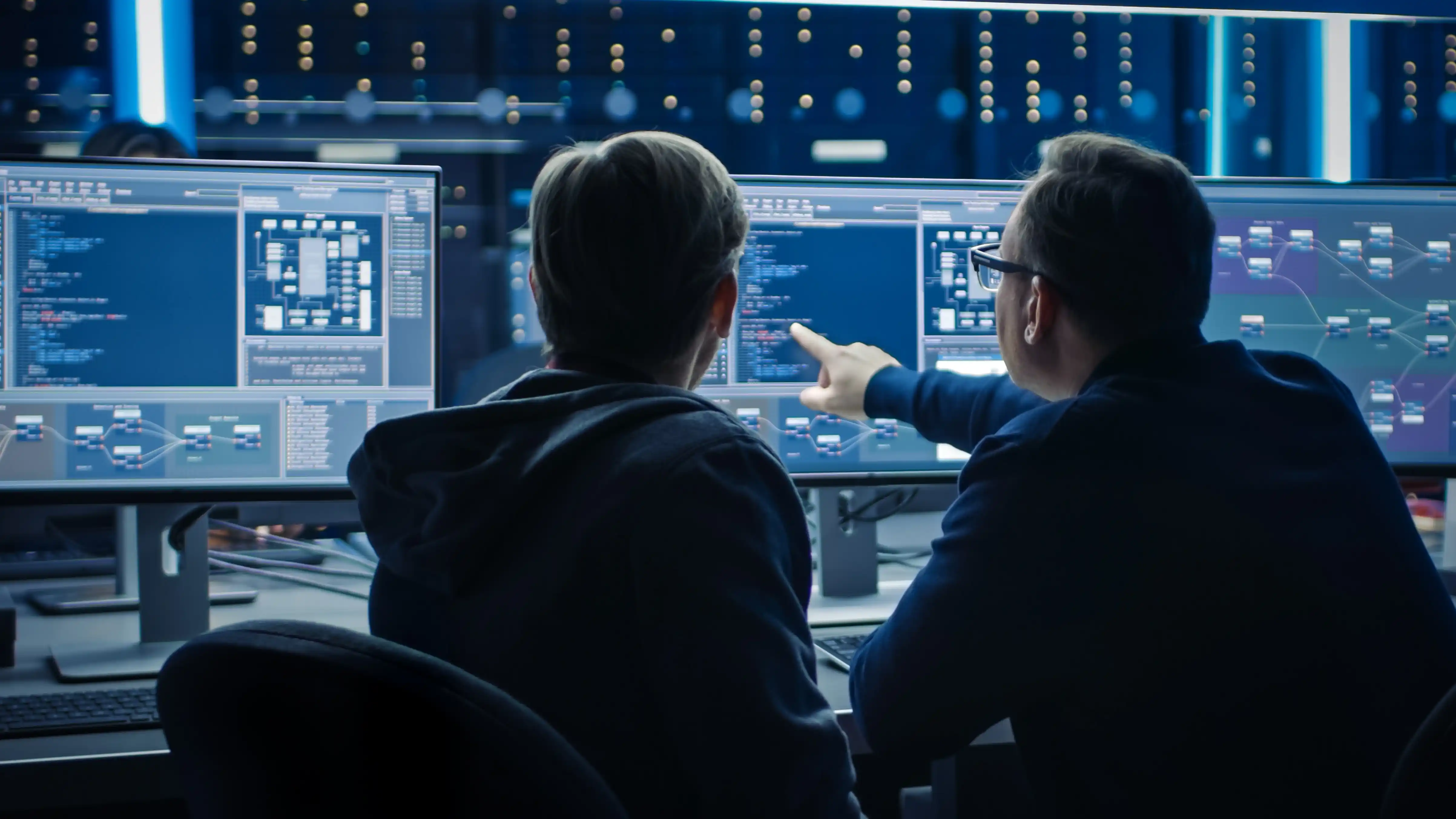
Maintenance-free operation
Exertherm’s sensors do not require batteries, eliminating the need for periodic maintenance or battery replacement. This feature maximizes uptime and ensures that the sensors can operate continuously without any interruptions.

.png?width=35&height=27&name=Vector%20(1).png)
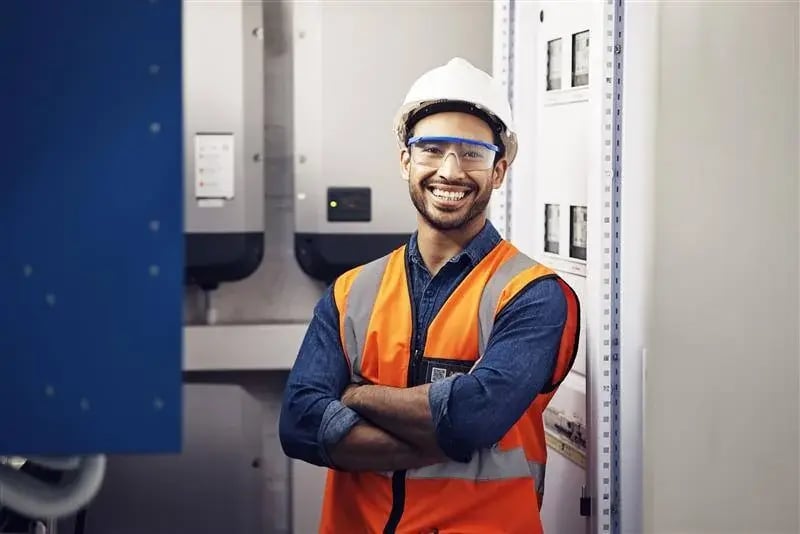
More accurate data via Delta T measurement
Exertherm’s sensors provide continuous measurement of critical joints or terminations, measuring Delta T (temperature rise over ambient) from within the switchgear enclosure. This approach offers several advantages:
Elimination of temperature correlation
Many sensors are limited due to only measuring the absolute temperature at the electrical joint. This can introduce the need for an additional ambient sensor, or temperature correlation, and Delta T calculations in a front-end system. Exertherm’s approach eliminates this, allowing for accurate alarm levels based on NETA guidelines.
Consistent and reliable data
By measuring Delta T directly, Exertherm’s sensors ensure consistent and reliable data across different panels and sites. This consistency is crucial for accurate monitoring and maintenance of electrical systems.
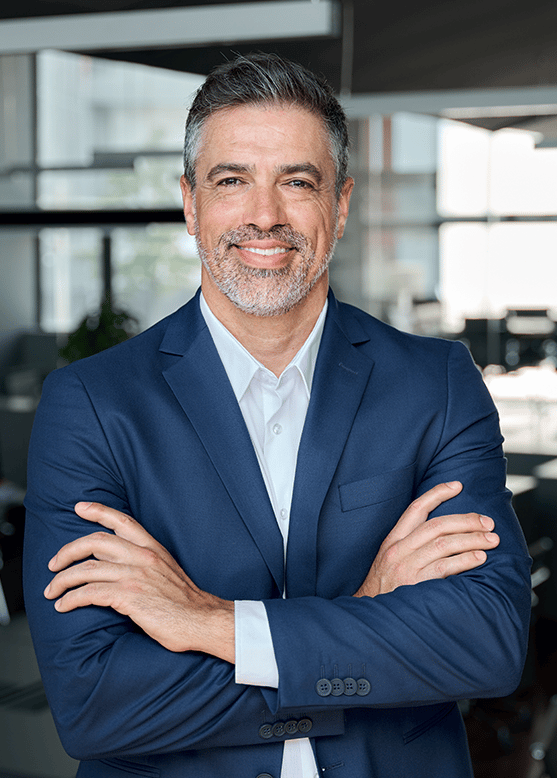
Considering load in monitoring
Load plays a crucial role in detecting compromised joints or terminations accurately. Exertherm’s LoadMap™ software, used alongside continuous thermal monitoring sensors, calculates alarm thresholds suitable for the maximum load on the monitored circuit. Here’s how this works:
Accurate detection at low loads
By utilizing temperature and load data, Exertherm’s system can detect compromised joints even at low loads. This capability is essential for early detection and prevention of potential issues.
Dynamic load data integration
Users can manually enter the maximum anticipated load or obtain dynamic load data via a metering device. This integration allows Exertherm’s sensors to provide load-based warning alarms, offering an enhanced level of 24x7 facility protection.
Enhanced facility protection
By considering load in its monitoring approach, Exertherm provides a comprehensive solution that enhances the safety and efficiency of electrical systems. This feature ensures that the system can operate at optimal levels without the risk of overloading or compromising the integrity of the connections.
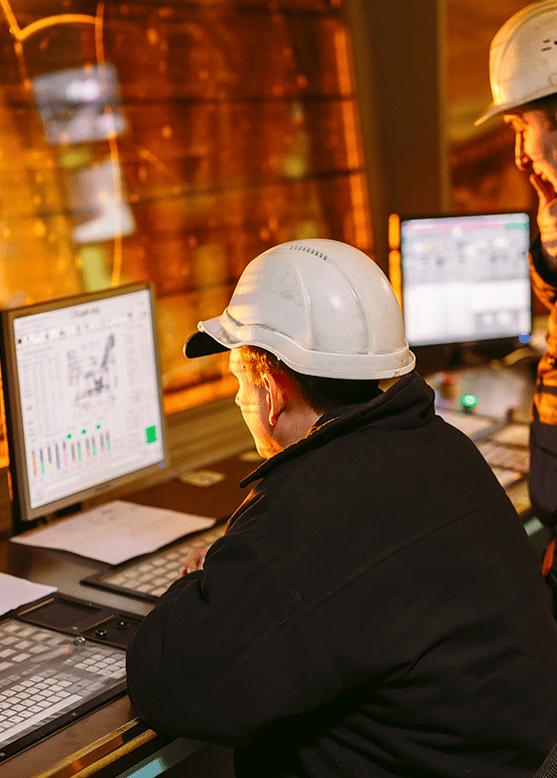
Permanently installed and requiring no power supply, Continuous Thermal Monitoring (CTM) sensors are at the forefront of predictive asset maintenance
It represents a significant advancement in the management of critical electrical assets. Our innovative approach to predictive maintenance is transforming digitization of electrical equipment with precision and efficiency, setting us apart from our competitors.
Exertherm's Continuous Thermal Monitoring (CTM) technology ensures reliability, security, and efficiency of electrical systems and personnel safety for organizations looking to optimize their asset management strategies.
With CTM, real-time data from sensors embedded in assets allows for 24x7 monitoring, detecting anomalies, and only triggering a call for maintenance when it's necessary. Whether it’s the contactless sensor placement, hard-wired communication, powerless operation, accurate Delta-T measurement, or load-based monitoring, Exertherm’s technology provides a robust and comprehensive solution for electrical asset management.
For organizations looking to enhance their maintenance strategies and ensure the optimal performance of their electrical systems, Exertherm’s continuous thermal monitoring technology is the clear choice.